The Duty of Defoamers in Enhancing Item Top Quality and Efficiency
Defoamers serve as essential ingredients that reduce this issue, making certain smoother production process while improving the visual and functional features of the final items. The selection of the proper defoamer can be vital to attaining optimum outcomes, elevating vital inquiries regarding formula compatibility and efficiency metrics that warrant more expedition.
Understanding Defoamers
Comprehending the duty of defoamers is vital for maintaining product quality across various sectors. Defoamers are chemical ingredients made to prevent the formation and decrease of foam in fluid systems, which can detrimentally impact procedures such as mixing, loading, and surface area stress. Foaming can cause inefficiencies, product problems, and compromised visual charm, making defoamers an essential part in manufacturing procedures.
In industrial applications, defoamers aid to improve product consistency and security. The efficient usage of defoamers not just makes sure smoother production processes however also adds to exceptional item performance.
In addition, the choice and formulation of a defoamer have to line up with particular application requirements, such as compatibility with other components, performance under differing temperature and pH conditions, and prospective regulatory restrictions. Eventually, understanding defoamers' features and their significance in numerous formulations is crucial for enhancing manufacturing and making sure the best quality end products.
Kinds Of Defoamers
Defoamers can be categorized right into numerous kinds based upon their composition and mechanism of action. The main kinds consist of silicone-based, non-silicone organic, and inorganic defoamers.
Silicone-based defoamers are among the most reliable, primarily due to their ability to spread out quickly on the liquid surface area and interfere with foam formation. Their special chemical framework permits remarkable stability, making them ideal for high-temperature applications and environments with varying pH levels.
Non-silicone organic defoamers, typically made up of all-natural oils or fats, are valued for their biodegradability and reduced toxicity. These are typically used in food and drink applications where safety and environmental impact are paramount.
Inorganic defoamers, which include compounds like talc or calcium carbonate, act by enhancing the thickness of the fluid, thereby reducing foam security. They are often used in commercial processes where compatibility with various other materials is not a worry.
Each sort of defoamer has distinctive benefits and constraints, permitting tailored remedies relying on the specific lathering issues experienced in numerous applications. Understanding these distinctions is important for optimizing performance and attaining desired item quality.
Applications Throughout Industries
Numerous markets leverage defoamers to enhance item high quality and operational performance. In the food and drink industry, defoamers are important in procedures such as developing and milk manufacturing to protect against foam development, which can result in inadequacies and item disparity. By controlling foam, manufacturers can make certain much better return and an extra uniform product.
In the pharmaceutical market, defoamers play a crucial function in the formulation of fluid medicines, where excessive foam can hinder this article mixing and accurate application. Their use aids maintain the stability of the formulations and promotes smoother production procedures.
The paint and coverings sector also counts on defoamers to improve the performance of products throughout application. By lessening foam, these ingredients make sure a smoother coating and boost the visual high qualities of the final item.

Advantages of Making Use Of Defoamers
While the application of defoamers varies across sectors, their benefits consistently enhance item top quality and process effectiveness. One substantial advantage is the reduction of foam formation during producing processes, which can or else lead to manufacturing delays and incongruities in product high quality. By minimizing foam, defoamers make it possible for a smoother circulation of materials, facilitating extra effective operations and lowering the chance of devices breakdowns.
In addition, making use of defoamers can improve the look and structure of last items. In markets such as coatings, paints, and food handling, too much foam can endanger the visual aesthetic appeals and overall quality, while the ideal defoamer application guarantees an uniform coating and desirable characteristics. Defoamers can add to set you back financial savings by decreasing waste during production and optimizing the use of raw materials.

Selecting the Right Defoamer
Choosing the ideal defoamer is essential for enhancing production procedures and guaranteeing product high quality. The option of defoamer affects not only the efficiency of foam control however additionally the overall performance attributes of the end product. Variables to think about consist of the kind of application, the chemistry of the solution, and the ecological problems under which the item will be used.
Different industries might call for details defoamer kinds, such as silicone-based, organic, or polymeric defoamers. Recognizing the compatibility of the defoamer with the key active ingredients is important to avoid unfavorable responses that can compromise item stability. Furthermore, the defoamer's performance in various temperature levels and pH levels should be assessed to guarantee constant performance.
Checking the defoamer in small-scale applications can give useful understandings right into its performance and viability. Consideration of governing compliance, especially in food, pharmaceuticals, and cosmetics, is paramount in choosing a defoamer. Inevitably, a detailed assessment of these factors will certainly lead to the option of a defoamer that not only regulates foam efficiently but also enhances the high quality and performance of the last product.
Verdict
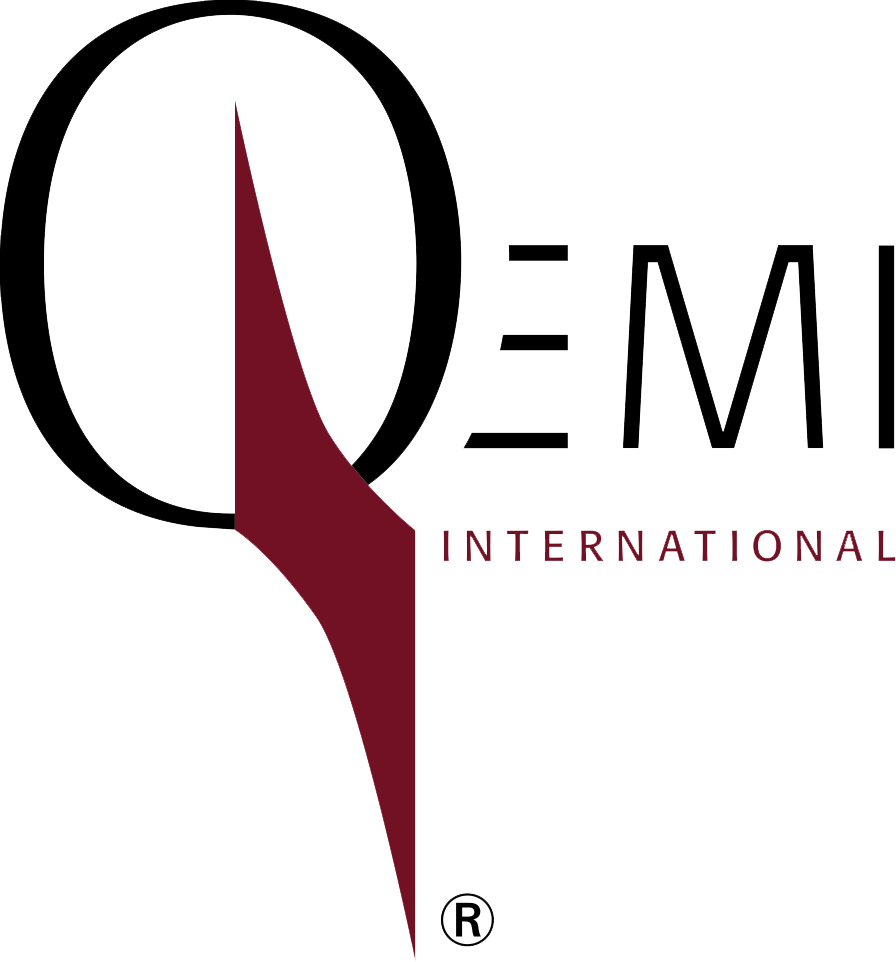
In conclusion, defoamers are necessary ingredients that significantly enhance item quality and performance throughout different sectors. By properly minimizing foam development, these representatives not only improve functional efficiency however also add to the aesthetic and useful stability of items. The tactical selection and application of defoamers cause set you back savings, maximized source use, and raised customer satisfaction. On the whole, the relevance of defoamers in commercial processes can not be overemphasized, as they play a crucial duty in achieving constant and premium results.
Foaming can lead to inefficiencies, product issues, and compromised visual allure, making defoamers an important component in making operations.
